Control cables are an essential component in various industries, providing a means to transmit signals and commands to operate machinery and equipment efficiently. The demand for high-quality control cables has been on the rise as industries continue to advance and require more sophisticated control systems. Control cable manufacturers play a crucial role in meeting this demand by producing reliable and durable cables that meet the specific requirements of different applications.
In this comprehensive guide, we will delve into the world of control cable manufacturers, exploring their role in the industry, the different types of control cables they produce, the manufacturing processes involved, quality standards, and the key players in the market.
Role of Control Cable Manufacturers
Control cable manufacturers are responsible for designing, producing, and supplying a wide range of control cables used in industries such as automotive, aerospace, telecommunications, robotics, and more. These manufacturers play a vital role in ensuring that machinery and equipment function smoothly and efficiently by providing high-quality cables that meet stringent performance requirements.
One of the primary responsibilities of control cable manufacturers is to understand the specific needs of their customers and develop customized solutions to meet those requirements. This involves collaborating closely with engineers, designers, and end-users to design cables that are tailored to the application at hand. Whether it's a simple on/off switch or a complex control system, control cable manufacturers must be able to produce cables that can transmit signals accurately and reliably.
Types of Control Cables
Control cables come in various types and configurations, each designed for specific applications and environments. Some of the most common types of control cables include:
1. Multi-Conductor Control Cables: These cables consist of multiple insulated conductors bundled together in a single cable jacket. They are commonly used in industrial applications where multiple signals need to be transmitted simultaneously.
2. Single-Conductor Control Cables: Single-conductor control cables consist of a single insulated conductor surrounded by a protective jacket. These cables are often used in applications where signal interference is a concern.
3. Armored Control Cables: Armored control cables feature an additional layer of protection, usually made of steel or aluminum, to shield the cables from external damage and environmental factors. These cables are commonly used in harsh industrial environments.
4. Flexible Control Cables: Flexible control cable s are designed to withstand bending and twisting without compromising signal transmission. They are ideal for applications that require cables to be routed through tight spaces or moving parts.
Manufacturing Processes
Control cable manufacturers employ a variety of manufacturing processes to produce high-quality cables that meet industry standards and performance requirements. Some of the key manufacturing processes involved in the production of control cables include:
1. Wire Drawing: The first step in the manufacturing process involves drawing metal wire through a series of dies to reduce its diameter and increase its length. This process helps improve the conductivity and tensile strength of the wire.
2. Insulation Extrusion: Once the wire has been drawn, it is passed through an extrusion machine where a layer of insulation material, such as PVC or polyethylene, is applied around the conductor. The insulation helps protect the conductor from external factors and prevents signal interference.
3. Twisting and Braiding: In some cases, multiple insulated conductors are twisted together to form a multi-conductor cable. Braiding machines may also be used to add an additional layer of protection to the cable.
4. Jacketing: After the conductors have been insulated and twisted together, a protective jacket is applied to the entire cable to provide further protection against moisture, abrasion, and other environmental factors.
Quality Standards
Control cable manufacturers are required to adhere to strict quality standards to ensure that their products meet the performance requirements of their customers. Some of the key quality standards that control cable manufacturers must comply with include:
1. UL (Underwriters Laboratories) Standards: UL is a global safety certification company that sets standards for various products, including control cables. Manufacturers must meet UL standards to ensure the safety and reliability of their products.
2. ISO 9001: ISO 9001 is an international standard for quality management systems that helps organizations demonstrate their ability to consistently provide products and services that meet customer and regulatory requirements.
3. RoHS Compliance: The Restriction of Hazardous Substances (RoHS) directive restricts the use of certain hazardous substances in electrical and electronic equipment, including control cables. Manufacturers must ensure that their products are RoHS compliant to meet environmental regulations.
Key Players in the Market
The control cable manufacturing industry is highly competitive, with a wide range of manufacturers vying for market share. Some of the key players in the control cable manufacturing market include:
1. Belden Inc.: Belden is a leading manufacturer of signal transmission products, including control cables, for various industries such as industrial automation, telecommunications, and transportation.
2. Lapp Group: Lapp Group is a global supplier of cables, connectors, and accessories for industrial applications. They offer a wide range of control cables designed to meet the specific needs of their customers.
3. Nexans: Nexans is a multinational cable manufacturer that produces a variety of control cables for industries such as energy, infrastructure, and automotive. They are known for their high-quality and innovative cable solutions.
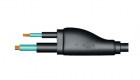
4. Prysmian Group: Prysmian Group is one of the largest cable manufacturers in the world, offering a comprehensive range of control cables for industrial, commercial, and residential applications. They are known for their advanced cable technologies and research and development capabilities.
Conclusion
Control cable manufacturers play a crucial role in providing the necessary connectivity solutions for a wide range of industries. By producing high-quality and reliable control cables that meet stringent performance requirements, these manufacturers help ensure the smooth and efficient operation of machinery and equipment in various applications.
From multi-conductor control cables to armored and flexible cables, control cable manufacturers offer a wide range of products designed to meet the specific needs of their customers. By adhering to strict quality standards and employing advanced manufacturing processes, these manufacturers continue to drive innovation and excellence in the control cable industry.
As industries continue to evolve and demand more sophisticated control systems, the role of control cable manufacturers will only become more critical. By staying at the forefront of technology and innovation, these manufacturers will continue to provide the connectivity solutions needed to power the industries of the future.